The Role of Robotics in Warehouse Automation
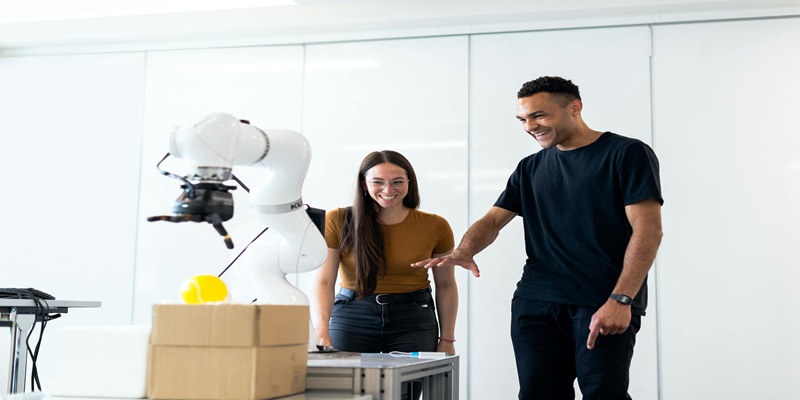
The logistics and supply chain industry has undergone a significant transformation, driven by advancements in technology. Among these advancements, robotics has emerged as a game-changer in warehouse automation. As businesses strive to meet the growing demands of e-commerce and faster delivery times, robotics has become an indispensable tool for optimizing warehouse operations.
Understanding Warehouse Automation
Warehouse automation refers to the use of technology and machinery to streamline and optimize warehouse operations. Traditionally, warehouses relied heavily on manual labor for tasks such as picking, packing, sorting, and transporting goods. However, with the rise of e-commerce and the need for faster order fulfillment, manual processes have become increasingly inefficient.
Automation addresses these inefficiencies by introducing systems that can perform repetitive tasks with greater speed, accuracy, and consistency. Robotics, in particular, has become a cornerstone of warehouse automation, enabling businesses to handle higher volumes of orders while reducing operational costs.
The Rise of Robotics in Warehouses
Robotics has revolutionized the way warehouses operate. From autonomous mobile robots (AMRs) to robotic arms, these machines are designed to perform a wide range of tasks with minimal human intervention. The adoption of robotics in warehouses has been fueled by several factors, including advancements in artificial intelligence (AI), machine learning, and sensor technology.
One of the most significant advantages of robotics is its ability to work alongside humans. Collaborative robots, or cobots, are designed to assist human workers by taking over physically demanding or repetitive tasks. This not only improves efficiency but also enhances workplace safety by reducing the risk of injuries.
Key Applications of Robotics in Warehouse Automation
Order Picking and Packing
Order picking is one of the most labor-intensive tasks in a warehouse. Traditionally, workers had to navigate through aisles to locate and retrieve items, which was time-consuming and prone to errors. Robotic systems, such as automated guided vehicles (AGVs) and robotic arms, have transformed this process.
AGVs can transport goods from one location to another, while robotic arms can pick and pack items with precision. These systems are often integrated with warehouse management software, allowing them to operate autonomously and adapt to changing demands.
Inventory Management
Accurate inventory management is crucial for maintaining optimal stock levels and avoiding overstocking or stockouts. Robotics plays a vital role in this area by automating inventory tracking and replenishment.
For instance, drones equipped with cameras and sensors can scan shelves to monitor stock levels in real-time. This data is then transmitted to a central system, which can generate alerts when items need to be restocked. By automating inventory management, businesses can reduce errors and improve overall efficiency.
Sorting and Transportation
Sorting and transporting goods are essential components of warehouse operations. Robotic systems, such as conveyor belts and sorting robots, can handle these tasks with remarkable speed and accuracy.
AMRs, for example, can navigate through warehouses using sensors and cameras to transport goods from one location to another. These robots are highly flexible and can be reprogrammed to adapt to new layouts or workflows, making them ideal for dynamic warehouse environments.
Quality Control and Inspection
Ensuring the quality of products is a critical aspect of warehouse operations. Robotic systems equipped with AI and machine learning algorithms can perform quality control checks with greater accuracy than human workers.
For example, robotic arms with high-resolution cameras can inspect products for defects or inconsistencies. If an issue is detected, the system can flag the item for further review or remove it from the production line. This not only improves product quality but also reduces waste and rework.
Benefits of Robotics in Warehouse Automation
Increased Efficiency
One of the most significant benefits of robotics is its ability to perform tasks faster and more accurately than humans. This leads to increased productivity and shorter order fulfillment times, which are critical in today’s fast-paced market.
Cost Savings
While the initial investment in robotics can be substantial, the long-term cost savings are significant. By automating repetitive tasks, businesses can reduce labor costs and minimize errors, which can lead to substantial savings over time.
Enhanced Accuracy
Human errors are inevitable in manual processes, but robotics can perform tasks with near-perfect accuracy. This is particularly important in areas such as order picking and inventory management, where mistakes can lead to costly delays or dissatisfied customers.
Improved Workplace Safety
Warehouse work can be physically demanding and hazardous. Robotics can take over dangerous tasks, such as lifting heavy objects or operating machinery, reducing the risk of workplace injuries.
Scalability
As businesses grow, their warehouse operations must scale accordingly. Robotics offers a scalable solution that can adapt to increasing demands without the need for significant additional labor.
Challenges of Implementing Robotics in Warehouses
While the benefits of robotics are undeniable, there are also challenges associated with its implementation.
High Initial Costs
The upfront cost of purchasing and installing robotic systems can be prohibitive for some businesses. Additionally, ongoing maintenance and software updates can add to the total cost of ownership.
Integration with Existing Systems
Integrating robotics with existing warehouse management systems can be complex and time-consuming. Businesses must ensure that their infrastructure is compatible with the new technology to avoid disruptions.
Workforce Adaptation
The introduction of robotics can lead to concerns about job displacement. While robotics can enhance productivity, businesses must also invest in training programs to help workers adapt to new roles and responsibilities.
Technical Limitations
Despite their advanced capabilities, robotic systems are not infallible. Technical issues, such as software glitches or hardware malfunctions, can disrupt operations and require immediate attention.
The Coming Opportunities of Robotics in Warehouse Automation
The future of robotics in warehouse automation looks promising, with continued advancements in AI, machine learning, and sensor technology. As these technologies transforms, robotic systems will become even more intelligent, versatile, and efficient. One emerging trend is the use of swarm robotics, where multiple robots work together to complete complex tasks. This approach can further enhance efficiency and flexibility in warehouse operations.
Another area of development is the integration of robotics with the Internet of Things (IoT). By connecting robotic systems to IoT networks, businesses can achieve greater visibility and control over their operations, enabling real-time decision-making and optimization.
Conclusion
Robotics has undoubtedly transformed the landscape of warehouse automation, offering numerous benefits such as increased efficiency, cost savings, and improved accuracy. However, businesses must also navigate challenges such as high initial costs and workforce adaptation to fully realize the potential of this technology. As the demand for faster and more efficient warehouse operations continues to grow, robotics will play an increasingly important role in shaping the future of the logistics industry. By embracing this technology, businesses can stay competitive and meet the transforming needs of their customers.